Hoisting systems for Iron Ore Mine Sishanling in China
3 Friction winder and further equipment
Customer
Benxi Longxin Mining Co., Ltd. (Jianlong Group)
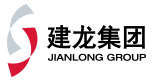
Country
China
The Sishanling iron ore mine is one of the largest iron ore mines currently being opened up in China. The Jianlong Group integrates new industries in the field of raw materials, steel, shipbuilding and electromechanics. In 2020 crude steel production in the group stood at about 37 million tonnes a year, so putting the company in eighth place amongst the world’s steel-producing companies.
Sishanling has 2.5 billion tonnes of proven iron ore reserves with an average iron content of about 31 %. Because of the concentrated ore body and its even distribution these reserves are suitable for
extraction on a large scale. They are the largest proven and registered iron ore deposits in China, having a long-term planned extraction capacity of 30 million tonnes a year. Initially 15 million tonnes will be
achieved a year in the next five years. In 2016 the project was included in the Ministry of Science and Technology’s „13th Five-Year Plan“ and declared a demonstration mine for research and application of
theory and technology for the exploitation of underground resources.
Year of commissioning
2023
Material to be conveyed
Iron ore
Technical data
6-Rope Friction Winder, tower-based
1500 m
6,75 m
55 t
7,5 Mio. t /p.a.
ST3-F, 12 pairs of brake elements BE250, Closed-Loop Technology
16 MW
6-Rope Friction Winder, floor-based
1500 m
6 m
ST3-F, 14 pairs of brake elements BE125, Closed-Loop Technology
3 MW
4-Rope Friction Winder, floor-based
1500 m
4,5 m
ST3-F, 6 pairs of brake elements BE125, Closed-Loop Technology
1 MW
Further information on delivered equipment
- Overall 7 sets indirect converters (IGBT)
- Automation equipment including machine control system
- Energy distribution systems
- Controls shaft signalling
- Controls loading and unloading
Overall 5 sets of rope sheaves for rope deflection
Comprehensive Consulting by SIEMAG TECBERG
After the customer and the design institute initially planned a total of three production shafts to be able to extract a total of 15 million tonnes a year at the first stage, after intense consultation with SIEMAG TECBERG the concept was optimised to two shafts each yielding 7.5 million tonnes a year. A service shaft equipped with a total of two service winders for the transport of personnel and machinery will also be sunk..
The overall concept thus initially provides for a total of three hoisting systems: a double-skip production system in the production shaft in the form of a 6.75 m 6-rope machine and a cage counterweight system for personnel and machine transport in the form of a 6 m 6-rope machine and a smaller cage counterweight system for emergencies in the form of a 4 m 4-rope machine in the service shaft.
The special feature of the three hoisting systems is the central control system. The control room is located in the hall of the hoisting machine of the service shaft. In normal operation the hoisting systems in the production and service shaft are all in automatic lifting operation. Furthermore, the two systems in the service shaft are fitted with wireless communication devices that enable the hoisting equipment to be controlled from the cage direct. This enables personnel to reach different levels direct.