System integration
Joining mechanics, hydraulics, automation and drive technology.
For a system supplier, it is particularly important to coordinate the mechanics, hydraulics, and drive and automation technology of conveyor systems in a system-integrated manner. After the individual components have been parameterized, a system test with pre-optimization of the entire drive train in the various operating states with different acceleration and deceleration phases can be carried out during testing on the test bench in the assembly plant.
Testing and optimisation is also carried out at a standstill whilst applying torque. This comprehensive approach provides the foundation for reliable plant operation after assembly on site. Furthermore, by carrying out the optimisation of the individual components prior to delivery SIEMAG TECBERG is able to offer a significantly faster and more straightforward commissioning and start-up phase of the system once on site. These benefits subsequently translate into increased uptime once the system is in operation on site due to SIEMAG TECBERG’s comprehensive factory testing and commissioning programs.
Mechanics / Hydraulics
A component level inspection checks the dimensional accuracy of function relevant system dimensions, such as shaft/rope carrier, shaft/motor, shaft/bearing connections. When the complete hoisting machine is commissioned at the factory, the drive is rotatated and the rope carrier and brake are made ready for operation. Optimised quality assurance through testing of
- Measurement of the air gaps between the brake elements and the brake disc
- Concentricity measurements of the brake discs on the rope carrier
- Reduction of geometric unbalance
- Avoidance of eccentricity
- Verification of axial and radial forces
- Verification of spindle and shaft torsion
- Reduction of excessive dynamic vibrations and noise development
- Checking of operating temperatures in slide and roller bearings
- Determination of the operating behaviour (temperature, pressure, etc.) of units
- Verification of the operational behaviour of gear units and clutches in use
- Factory adjustment of the complete brake system, incl. analysis of brake curves
Automation and drive technology
An interface verification of mechanics, hydraulics, automation, inverter system, auxiliary controls, as well as a process simulation for testing sequence controls and the control of different operating modes is carried out.
- The interaction between automation and the braking system on the "rotating system" is checked
- The controllers are parameterised
A process simulation is carried out to test control sequences and correct operation of the various operating modes. Optimisation of the entire electric drive concept with regard to the total moment of inertia:
- Analysis of motor characteristics, e.g. insulation and resistance measurements, no-load characteristics at nominal voltage
- Heating under load
- Testing and optimisation of the motor and control behaviour at standstill torque (speed n = 0)
- Testing of the behaviour at different starting torques, load jumps and load cycles
Improved customer benefit thanks to System Factory Acceptance Test (FAT)
- Significantly increased functional safety for the overall system resulting from the integrated functional tests as described above
- System FAT offers customers greater planning certainty for the entire mine production plan during the commissioning on site
- Reduced assembly and commissioning time on site thanks to factory setup and factory commissioning (parameterisation)
- Variant simulation for the optimisation of assembly and commissioning on-site as support for customer planning
- Documentation of system parameters is available earlier to support approvals and certifications
- Improved process descriptions for the erection of the plant through modularisation of assembly and commissioning processes
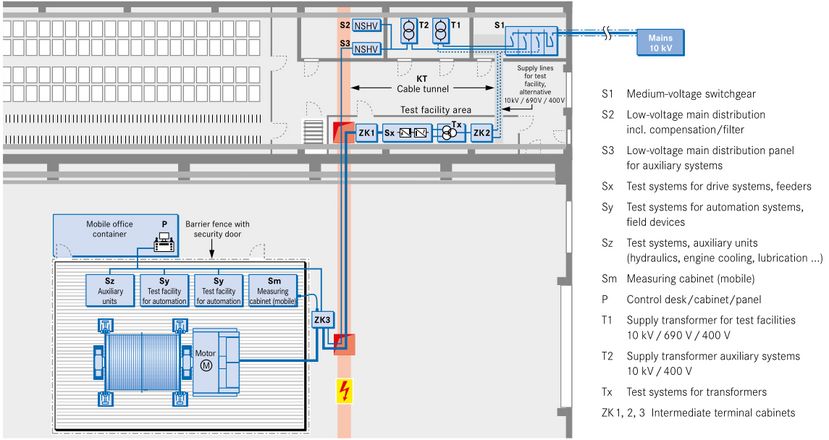